熔模铸造常见缺陷及原因分析(铸造缺陷术语大全)
一、多肉类缺陷
多肉类缺陷铸件表面各种多肉缺陷的总称。
注:包括飞翅、毛刺﹑抬型﹑胀砂﹑冲砂、掉砂,外渗物等。
1.1飞翅(飞边) 垂直于铸件表面上厚薄不均匀的薄片状金属突起物。
注:常出现在铸件分型面和芯头部位。
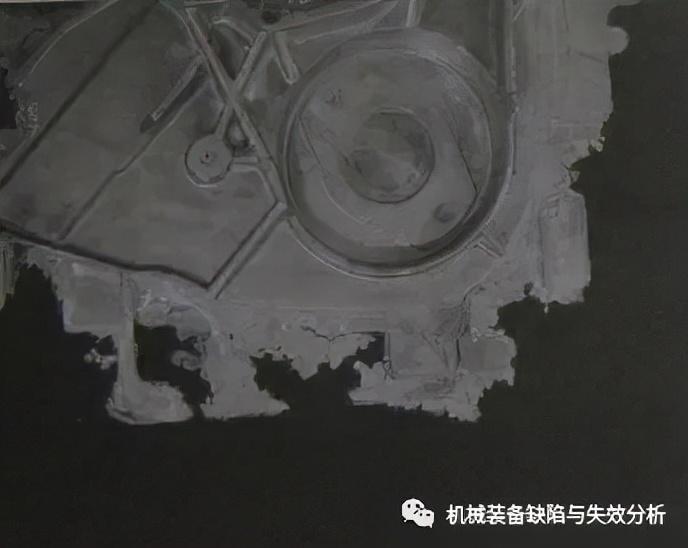
1.2毛刺 铸件表面上刺状金属突起物。
注:常出现在型和芯的裂缝处,形状极不规则。呈网状或脉状分布的毛刺称脉纹。
1.3外渗物(外渗豆)铸件表面渗出来的金属物。
注:多呈豆粒状,一般出现在铸件的自由表面上,如明浇铸件的上表面、离心浇注铸件的内表面等。其化学成分与铸件金属往往有差异。
1.4粘模多肉 因砂型(芯)起模时部分砂块粘附在模样或芯盒上所引起的铸件相应部位多肉。
1.5冲砂 砂型(芯)表面局部型砂被金属液冲刷掉,在铸件表面的相应部位上形成的粗糙、不规则的金属瘤状物。
注:常位于浇口附近﹐被冲刷掉的型砂,往往在铸件的其他部位形成砂眼。
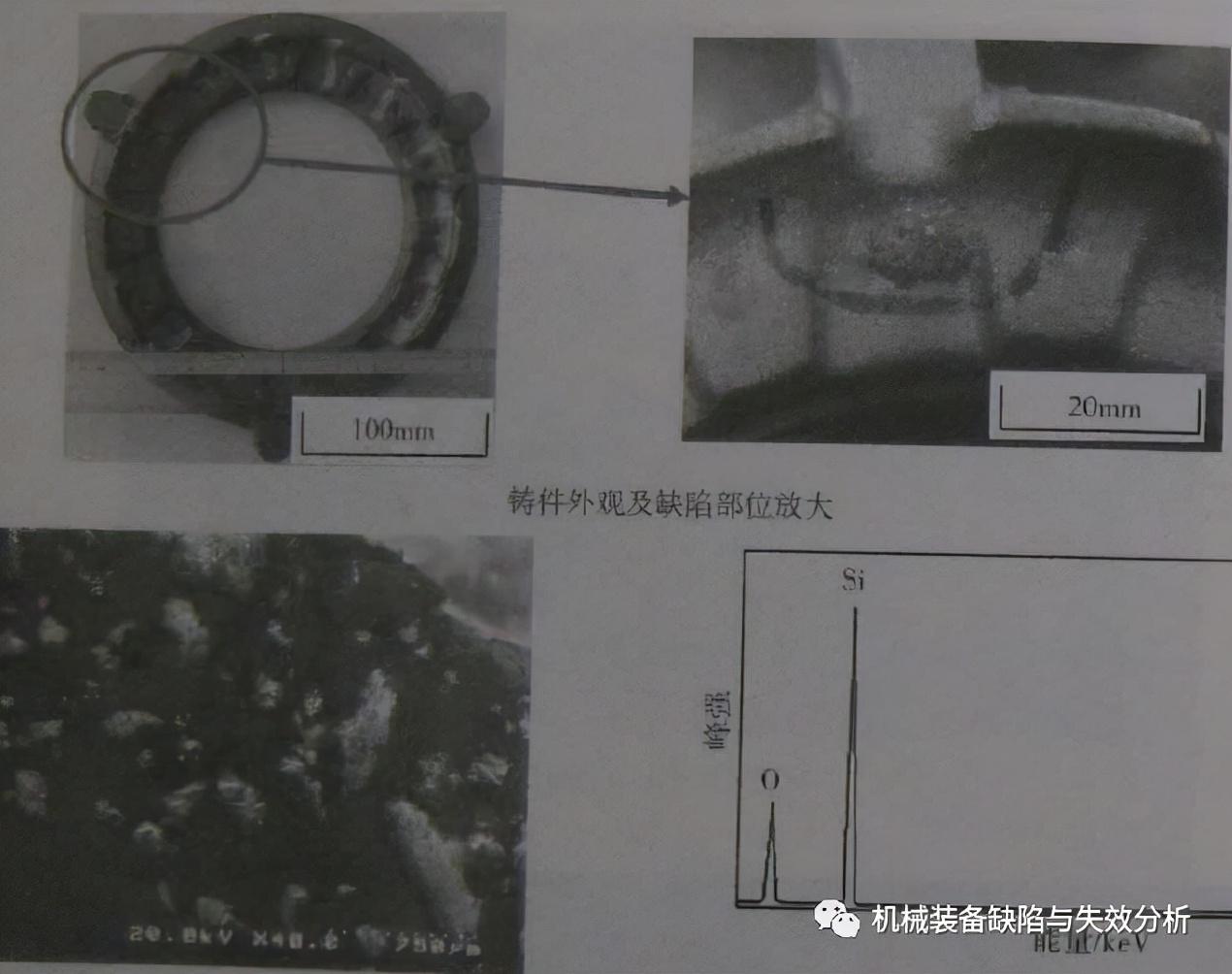
1.6 掉砂砂型(芯)的局部砂块在机械力作用下掉落,使铸件表面相应部位形成的块状金属突起物。
注:其外形与掉落的砂块很相似。在铸件其他部位则往往出现砂眼或残缺。
1.7 胀砂 铸件内外表面局部胀大,重量增加的现象。由型壁退移引起。
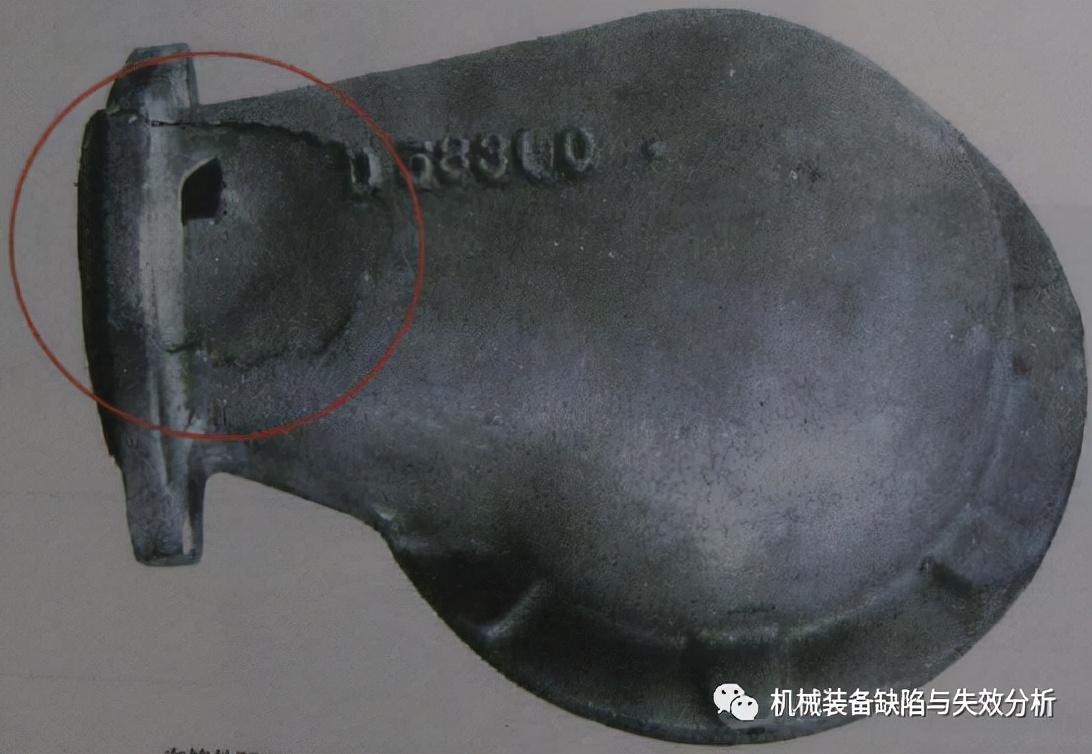
1.8 抬型(抬箱) 由于金属液的浮力使上型或砂芯局部或全部抬起、使铸件高度增加的现象。
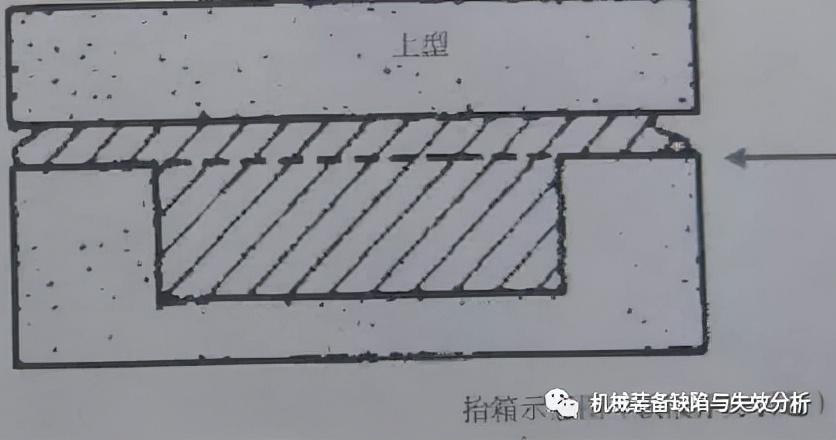
二、孔洞类缺陷
在铸件表面和内部产生的不同大小、形状的孔洞缺陷的总称。注:包括气孔,缩孔、缩松等。
2.1 气孔 铸件内由气体形成的孔洞类缺陷。
注:其表面一般比较光滑,主要呈梨形、圆形和椭圆形。一般不在铸件表面露出,大孔常孤立存在,小孔则成群出现。
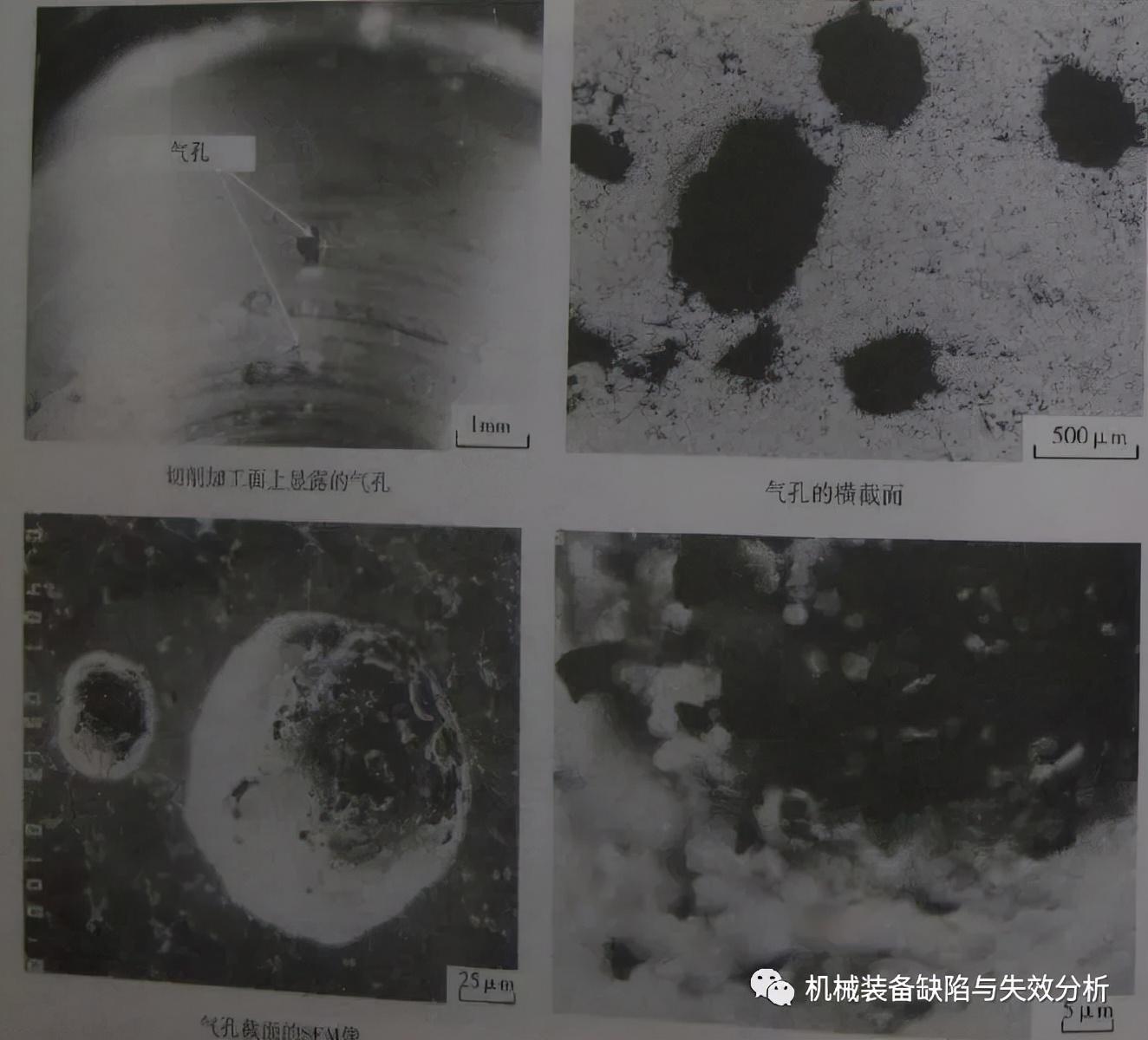
2.2 气缩孔 分散性气孔与缩孔和缩松合并而成的孔洞类铸造缺陷。
2.3 针孔 一般为针头大小分布在铸件截面上的析出性气孔。注:铝合金铸件中常出现这类气孔,对铸件性能危害很大。
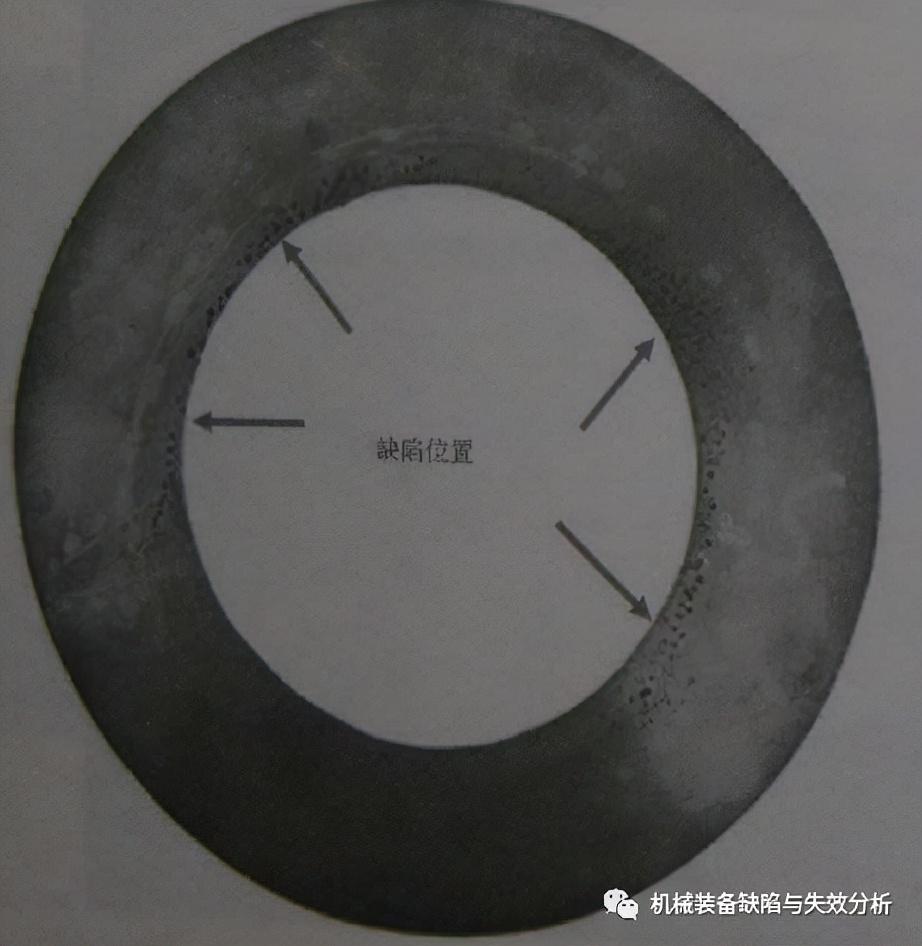
2.4 表面针孔 成群分布在铸件表层的分散性气孔。
注:其特征和形成原因与皮下气孔相同,通常暴露在铸件表面,机械加工1 mm~2 mm后即可去掉。
2.5 皮下气孔 位于铸件表皮下的分散性气孔。
注:其为金属液与砂型之间发生化学反应产生的反应性气孔。形状有针状.螂蚂状.球状,梨状等。大小不一,深度不等。通常在机械加工或热处理后才能发现。
2.6 呛火 浇注过程中产生的大量气体不能顺利排出,在金属液内发生沸腾,导致在铸件内产生大量气孔,甚至出现铸件不完整的缺陷。
三、收缩缺陷
金属凝固收缩时﹐由于金属液未对铸件有效补缩而产生的缺陷。注:包括缩孔、缩松﹑缩陷、缩沉等。
3.1 缩孔 铸件在凝固过程中,由于补缩不良而产生的孔洞。
注:其形状极不规则,孔壁粗糙并带有枝状晶,常出现在铸件最后凝固的部位。广义的缩孔包括缩松。
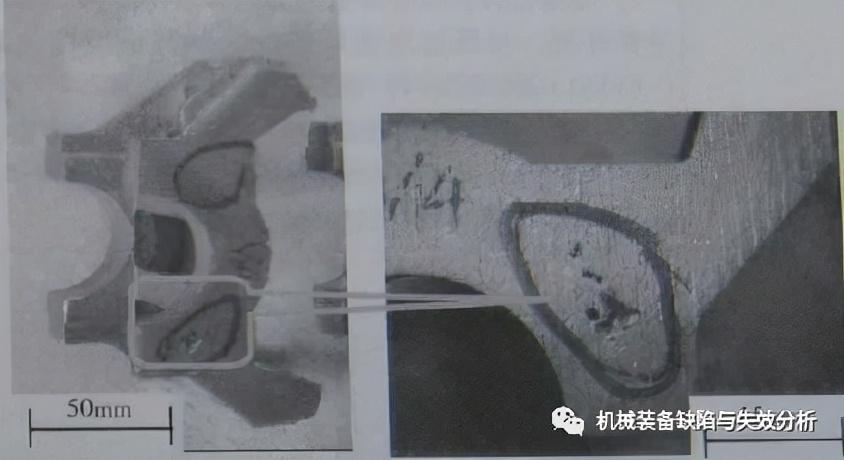
3.2 缩松 铸件断面上出现的分散而细小的缩孔。
注:借助高倍放大镜才能发现的缩松称为显微缩松。铸件有缩松缺陷的部位,在气密性试验时易渗漏。

3.3 疏松(显微缩松) 铸件缓慢凝固区出现的很细小的孔洞。
注:分布在枝晶内和枝晶间。是弥散性气孔,显微缩松、组织粗大的混合缺陷,使铸件致密性降低,易造成渗漏。
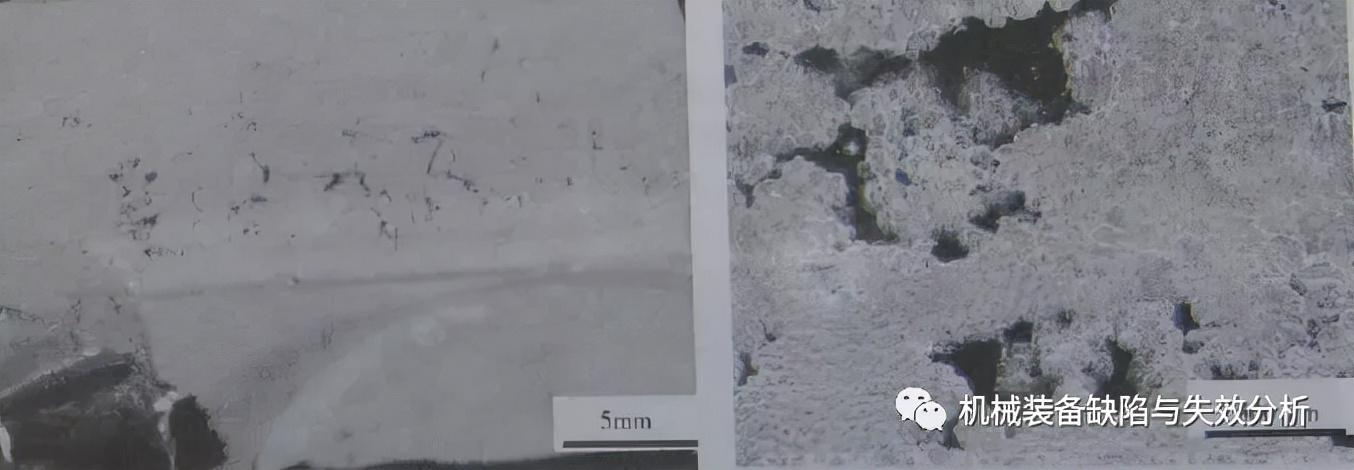
3.4 渗漏 铸件在气密性试验时或使用过程中发生的漏气、渗水或渗油现象。注:多由于铸件有缩松﹑疏松﹑组织粗大、毛细裂纹、气孔或夹杂物等缺陷引起。
四、裂纹.冷隔类缺陷
裂纹 铸件表面或内部由于各种原因发生断裂而形成的条纹状裂缝,包括热裂,冷裂、热处理裂纹等。
4.1 冷裂 铸件凝固后在较低温度下由铸造应力导致的裂纹。注:裂口常穿过晶粒延伸到整个断面。
4.2 热裂 铸件在凝固后期或凝固后在较高温度下形成的裂纹。
注:其断面严重氧化,无金属光泽,裂口沿晶粒边界产生和发展,外形曲折而不规则。
4.3 缩裂(收缩裂纹) 由于铸件补缩不当、收缩受阻或收缩不均匀而造成的裂纹。注:可能出现在刚凝固之后或在更低的温度。
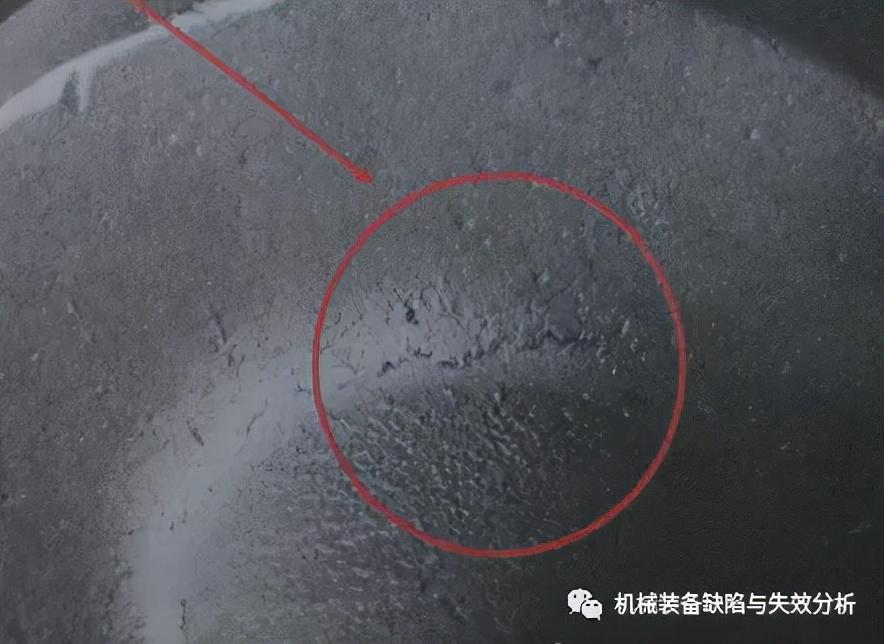
4.4 热处理裂纹 铸件在热处理过程中产生的穿透或不穿透的裂纹。
4.5 网状裂纹(龟裂) 金属型和压铸型因受交变热机械作用发生热疲劳,在型腔表面形成的微细龟壳状裂纹。铸型龟裂在铸件表面形成龟纹缺陷。
4.6 白点(发裂、发纹) 钢中主要因氢的析出而引起的缺陷。在纵向断面上,它呈现近似圆形或椭圆形的银白色斑点,故称白点;在横断面宏观磨片上,腐蚀后则呈现为毛细裂纹,故又称发裂。
4.7 冷隔 在铸件上穿透或不穿透的,边缘呈圆角状的缝隙。
注:多出现在远离浇口的宽大上表面或薄壁处,金属流汇合处,以及冷铁,芯撑等激冷部位。
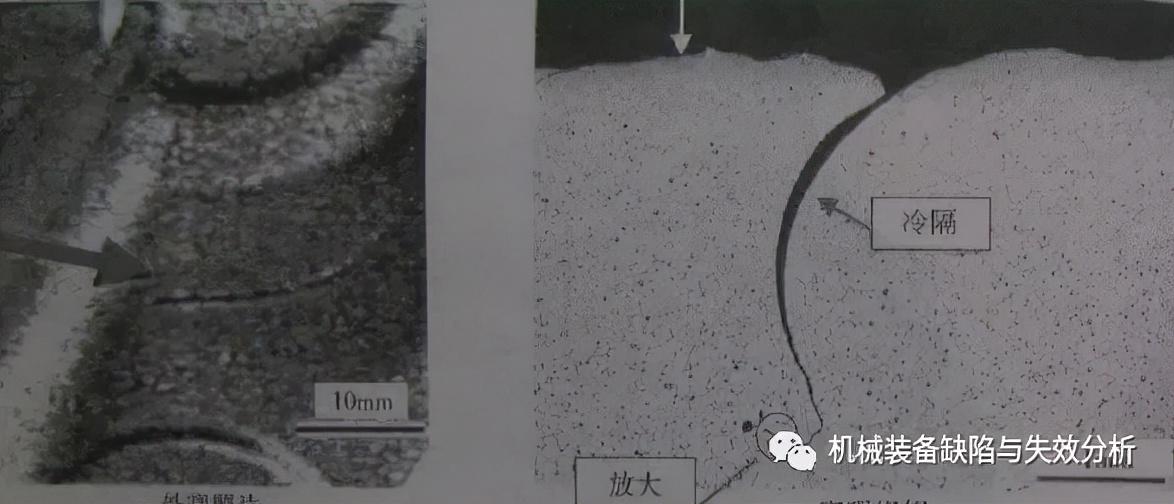
4.8 浇注断流 铸件表面某一高度可见的接缝。
注:接缝的某些部分熔合不好或分开。由浇注中断而引起。
4.9 重皮 充型过程中因金属液飞溅或液面波动,型腔表面已凝固金属不能与后续金属熔合所造成的铸件表皮折叠缺陷。
五、表面缺陷
表面缺陷铸件表面上产生的各种缺陷的总称,包括鼠尾、沟槽、夹砂结疤、粘砂、表面粗糙、皱皮、缩陷、桔皮面、斑点、印痕等。
5.1 表面粗糙 铸件表面毛糙、凹凸不平,其微观几何特征超出铸造表面粗糙度测量上限,但尚未形成粘砂缺陷。
5.2 粘砂 铸件表面或内腔粘附着一层难以清除的砂粒。分为机械粘砂和化学粘砂两类。

5.3 化学粘砂 铸件的部分或整个表面上牢固地粘附一层由金属氧化物、砂子和粘结剂相互作用而生成的低熔点化合物。
注:化学粘砂只能用砂轮磨去。

5.4 机械粘砂(渗透粘砂) 铸件的部分或整体表面上,粘附着一层砂粒和金属的机械混合物。注:清铲粘砂层时可以看到金属光泽。
5.5 夹砂结疤(夹砂)铸件表面产生的疤片状金属突起物。其表面粗糙,边缘锐利,有一小部分金属和铸件本体相连﹐把片状突起物与铸件之间有砂层。
5.6 涂料结疤 由于涂层在浇注过程中开裂,金属液进入裂缝,在铸件表面产生的疤痕状金属突起物。
5.7 沟槽 铸件表面产生较深(大于5 mm)的边缘光滑的V型凹痕。通常有分枝,多发生在铸件的上、下表面。
5.8 粘型 熔融金属粘附在金属型型腔表面的现象。
5.9 龟纹(网状花纹) 磁力探伤时熔模铸件表面出现的龟壳状网纹缺陷。多出现在铸件过热部位。因浇注温度和型壳温度过高,金属液与型壳内Na2О残留量过高而析出的“白霜”发生反应所致。或因铸型型腔表面龟裂而在金属型铸件或压铸件表面形成的网状花纹缺陷。
5.10 流痕(水纹) 压铸件表面与金属流动方向一致的,无发展趋势且与基体颜色明显不一样的微凸或微凹的条纹状缺陷。
5.11 缩陷 铸件的厚断面或断面交接处上平面的塌陷现象。
注:缩陷的下面,有时有缩孔。缩陷有时也出现在内缩孔附近的表面。
5.12 鼠尾 铸件表面出现较浅(小于或等于5 mm)的带有锐角的凹痕。
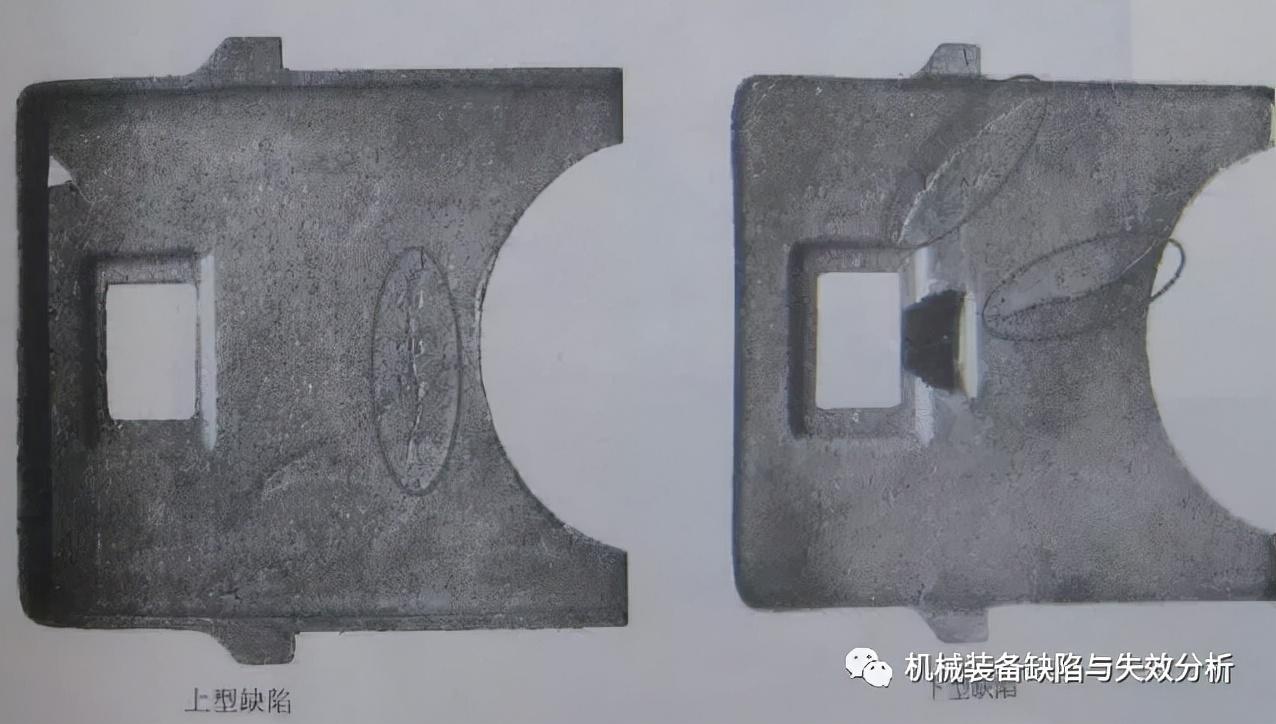
5.13 印痕 因顶杆或镶块与型腔表面不齐平,而在金属型铸件或压铸件表面相应部位产生的凸起或凹下的痕迹。
5.14 皱皮 铸件上不规则的粗粒状或皱摺状的表皮。一般带有较深的网状沟槽。
5.15 拉伤 金属型铸件和压铸件表面由于与金属型啮合或粘结,顶出时顺出型方向出现的擦伤。
六、残缺类缺陷
铸件由于各种原因造成的外形缺损缺陷的总称。包括浇不到,未浇满﹑型漏、跑火,损伤等。
6.1 浇不到(浇不足) 铸件残缺或轮廓不完整或可能完整但边角圆且光亮。常出现在远离浇口的部位及薄壁处。其浇注系统是满的。
6.2 未浇满 铸件上部产生缺肉,其边角略呈圆形,浇冒口顶面与铸件平齐。
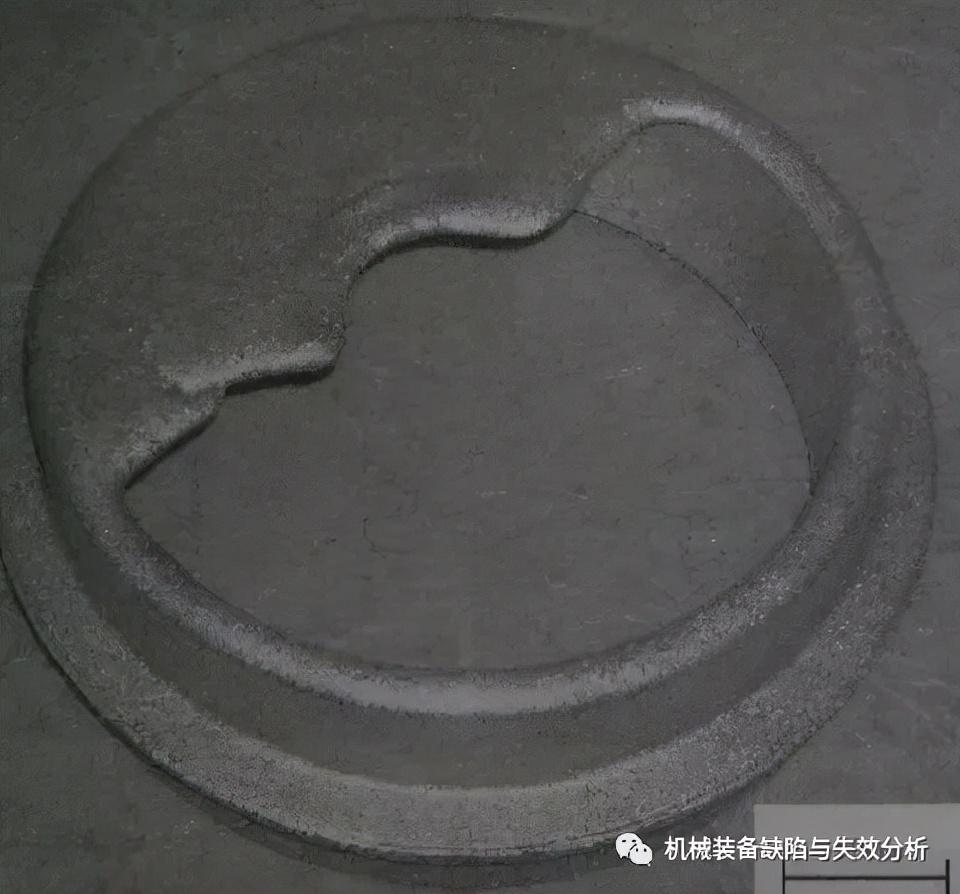
6.3 型漏(漏箱) 铸件内有严重的空壳状残缺。
注:有时铸件外形虽较完整,但内部的金属已漏空,铸件完全呈壳状,铸型底部有残留的多余金属。
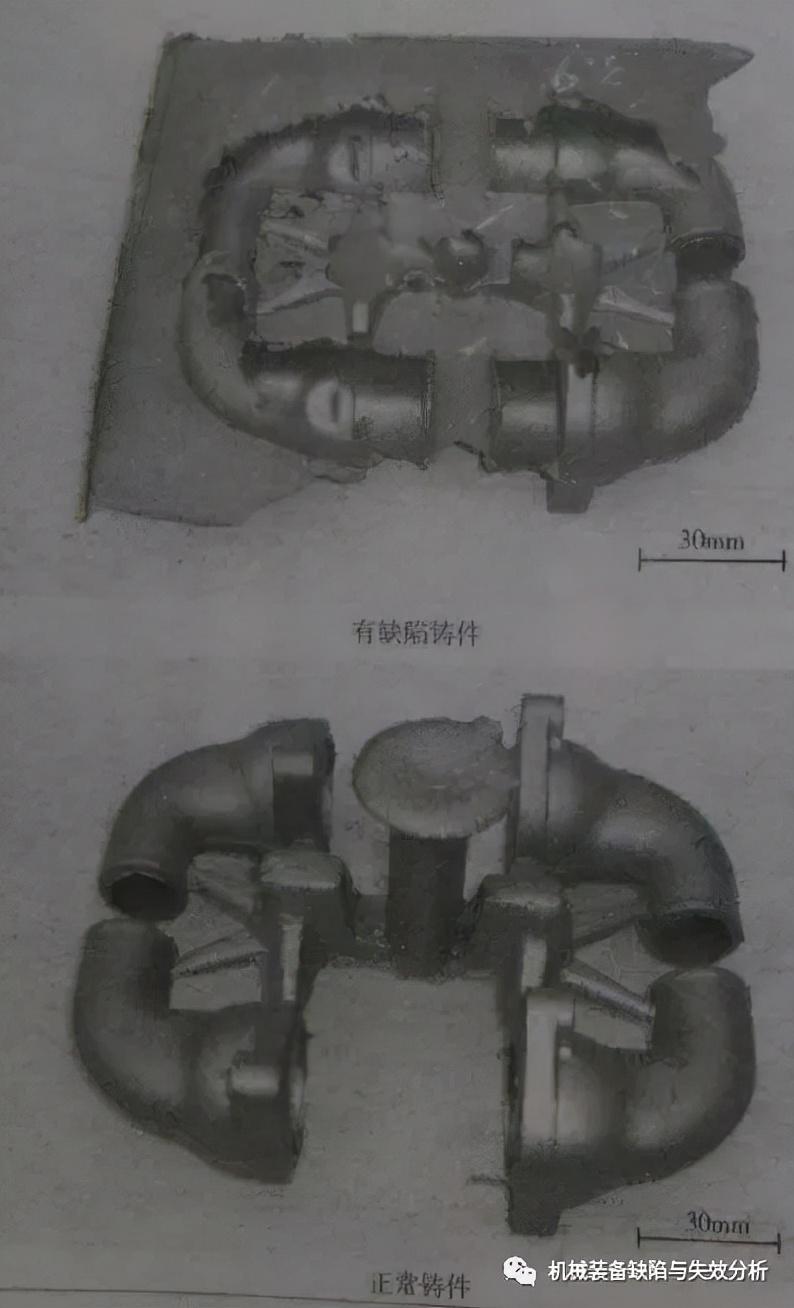
6.4 损伤(机械损伤)铸件受机械撞击而破损﹑残缺不完整的现象。
6.5 跑火 因浇注过程中金属液从分型面处流出而产生的铸件分型面以上部分严重凹陷和残缺有时会沿未充满的型腔表面留下类似飞翅的残片。
6.6 漏空 在低压铸造中,由于结晶时间过短﹐金属液从升液管漏出,形成类似型漏的缺陷。
七、形状及重量差错类缺陷
7.1 铸件变形 铸件在铸造应力和残余应力作用下所发生的变形及由于模样或铸型变形引起的变形。
7.2 形状不合格 铸件的几何形状不符合铸件图的要求。
7.3 尺寸不合格 在铸造过程中由于各种原因造成的铸件局部尺寸或全部尺寸与铸件图的要求不符。
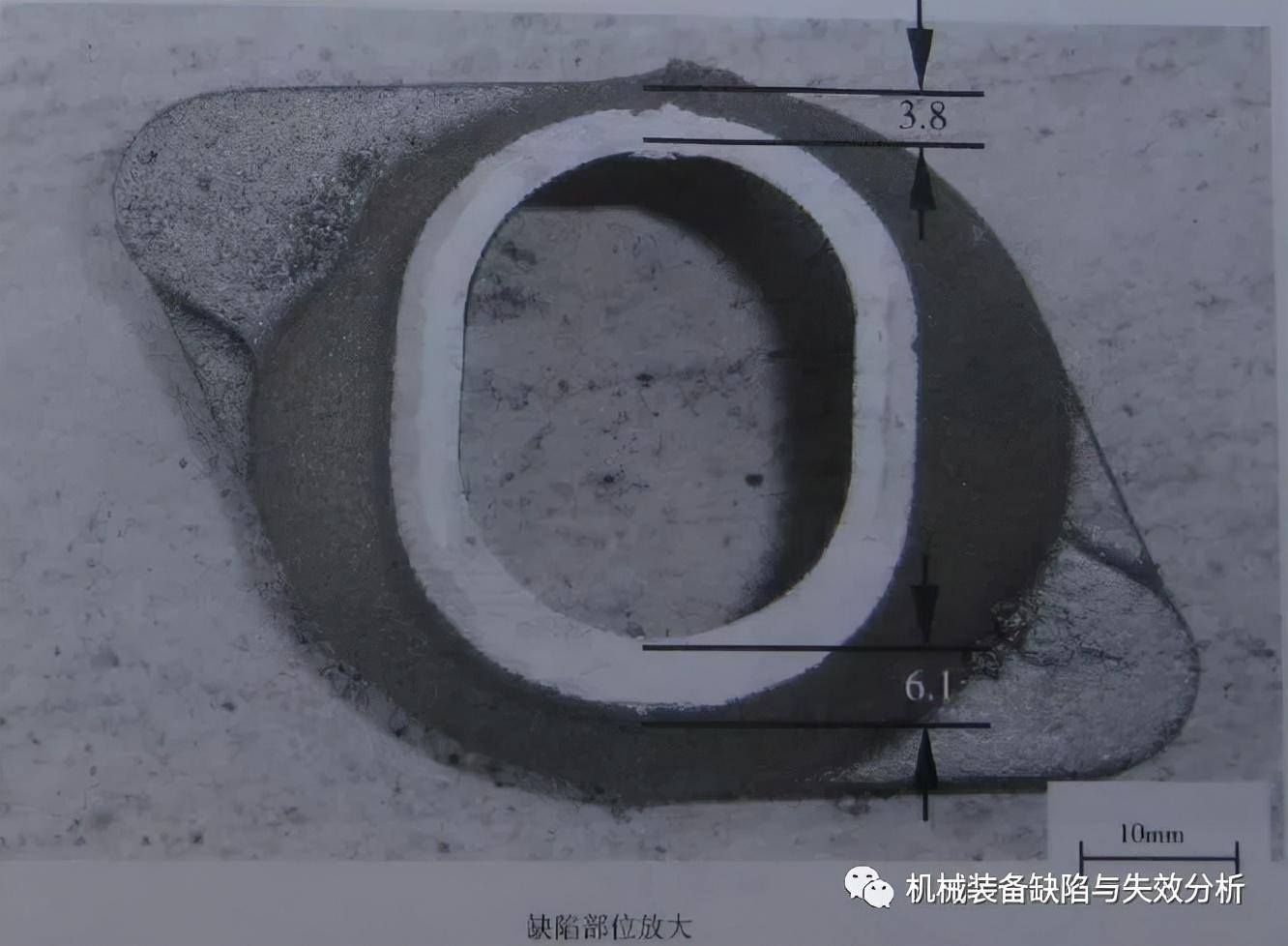
7.4 拉长 由于凝固收缩时铸型阻力大而造成的铸件部分尺寸比图样尺寸大的现象。
7.5 挠曲 铸件在生产过程中,由于残余应力,模样或铸型变形等原因造成的弯曲和扭曲变形。或铸件在热处理过程中因未放平正或在外力作用下而发生的弯曲和扭曲变形。
7.6 错型(错箱)由于合型时错位,铸件的一部分与另一部分在分型面处相互错开。
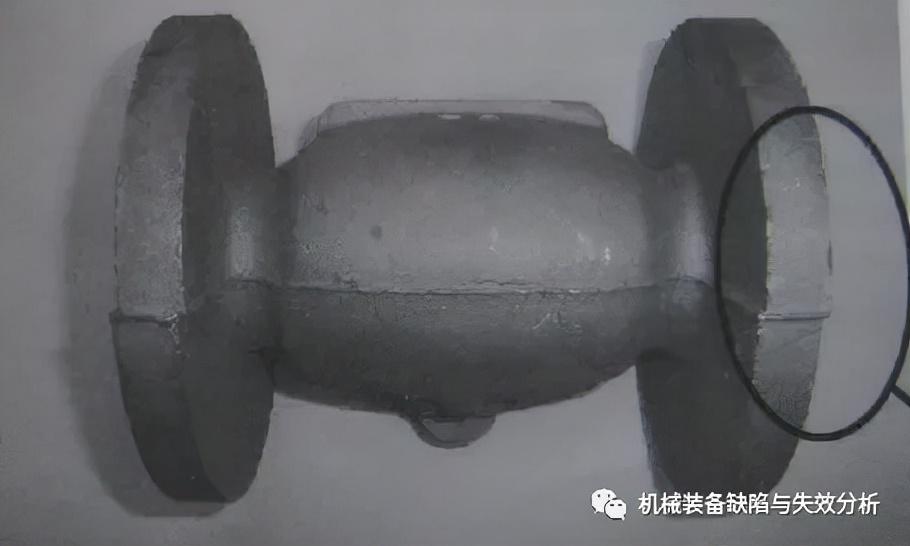
7.7 错芯 由于砂芯在分芯面处错开,铸件孔腔尺寸不符合铸件图的要求。
7.8 偏芯(漂芯)由于型芯在金属液作用下漂浮移动,使铸件内孔位置、形状和尺寸发生偏错,不符合铸件图的要求。
7.9 型芯下沉 由于芯砂强度低或芯骨软,不足以支撑自重,使型芯高度降低、下部变大或下弯变形而造成的铸件变形缺陷。
7.10 串皮 熔模铸件内腔中的型芯露在铸件表面﹐使铸件缺肉。
注:主要原因是型芯在型壳焙烧,浇注过程中移位、变形或折断,浇注后型芯偏离正常位置,露出铸件表面。浇注温度和型壳温度偏低﹑空心铸件壁厚过薄时,使金属液充填不满时也会造成露芯。
7.11 型壁移动 金属液浇入砂型后,型壁发生位移的现象。
注:造成型壁移动的原因有:金属液热作用使型壁膨胀;金属液压力和铸铁石墨化的膨胀力使砂型进一步被紧实。在同样的湿型条件下,型壁移动大小次序为:球墨铸铁>孕育灰铸铁>未孕育灰铸铁>铸钢>白口铸铁。
7.12舂移 由于舂移砂型或模样,在铸件相应部位产生的局部增厚缺陷。
注:其往往发生在春紧过度的砂型部位。主要原因是:已紧实的型砂受到单方向的过大紧实力作用而沿模样表面滑移,或模样活块移动等。
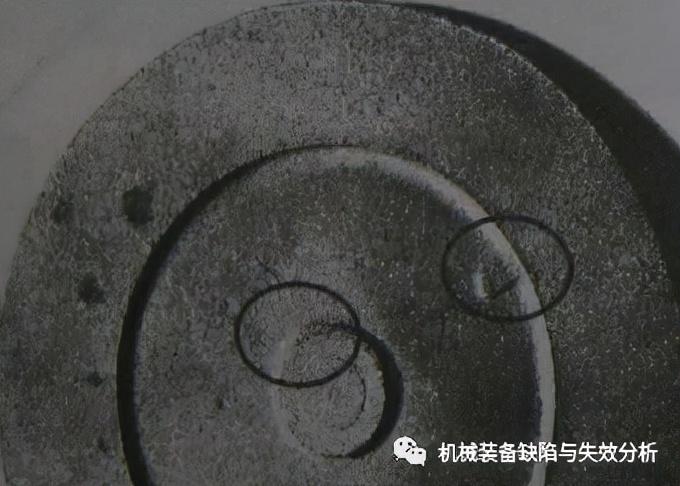
7.13 缩沉 使用水玻璃石灰石砂型生产铸件时产生的一种铸件缺陷,其特征为铸件断面尺寸胀大。
7.14 缩尺不符 由于制模时所用的缩尺与合金收缩不相符而产生的一种铸造缺陷。
7.15 坍流 离心铸造时,因转速低,停车过早、浇注温度过高等引起合金液逆旋转方向由上向下流淌或淋降,在离心铸件内表面形成的局部凹陷、凸起或小金属瘤。
7.16 铸件重量不合格(超重) 铸件实际重量相对于公称重量的偏差值超出铸件重量公差。
八、夹杂类缺陷
铸件中各种金属和非金属夹杂物的总称。
注:通常是氧化物、硫化物、硅酸盐等杂质颗粒机械地保留在固体金属内,或凝固时在金属内形成,或在凝固后的反应中,在金属内形成。包括夹杂物﹑冷豆、内渗豆、夹渣、砂眼等。
8.1 夹杂物 铸件内或表面上存在的和基体金属成分不同的质点。注:包括渣﹑砂、涂料层﹑氧化物﹑硫化物﹑硅酸盐等。
8.2 内生夹杂物 在熔炼、浇注和凝固过程中,因金属液成分之间或金属液与炉气之间发生化学反应而生成的夹杂物,以及因金属液温度下降,溶解度减小而析出的夹杂物。
8.3 外生夹杂物 由熔渣及外来杂质引起的夹杂物。
8.4 夹渣 因浇注金属液不纯净,或浇注方法和浇注系统不当,由裹在金属液中的熔渣,低熔点化合物及氧化物造成的铸件中夹杂类缺陷。
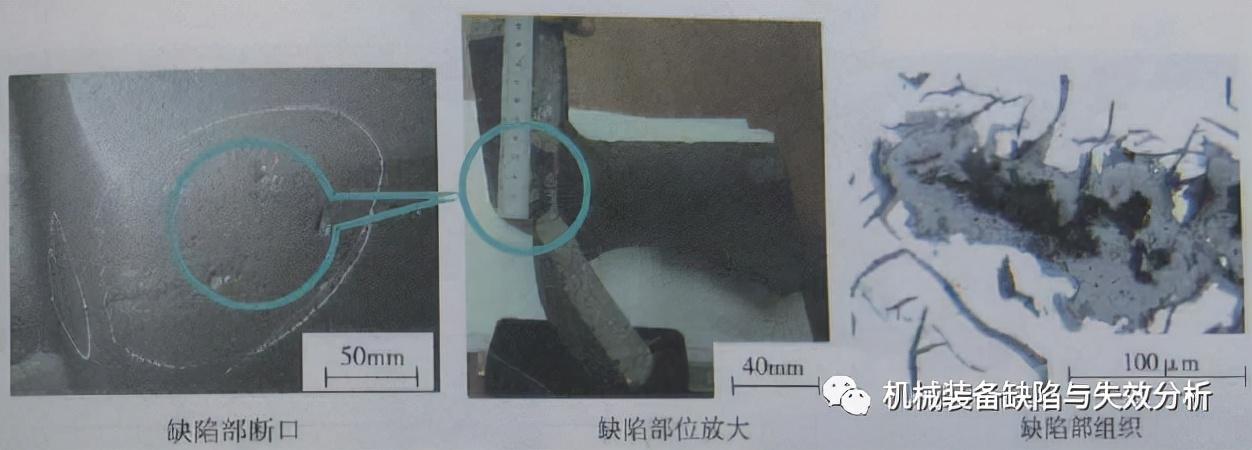
注:由于其熔点和密度通常都比金属液低,一般分布在铸件顶面或上部,以及型芯下表面和铸件死角处。断口无光泽呈暗灰色。
8.5 黑渣 球墨铸铁件中由硫化镁﹑硫化锰﹑氧化镁和氧化铁等组成的夹渣缺陷。注:其在铸件断面上呈暗灰色。一般分布在铸件上部、砂芯下表面和铸件死角处。

8.6 涂料渣孔 因涂层粉化﹑脱落后留在铸件表面而造成的,含有残留涂料堆积物质的不规则坑窝。
8.7 冷豆 浇注位置下方存在于铸件表面的金属珠。注:其化学成分与铸件相同,表面有氧化现象。

8.8 磷豆 含磷合金铸件表面渗析出来的豆粒或汗珠状磷共晶物。
8.9 内渗物(内渗豆) 铸件孔洞缺陷内部带有光泽的豆粒状金属渗出物。
注:其化学成分和铸件本体不一致,接近共晶成分。
8.10 砂眼 铸件内部或表面带有砂粒的孔洞。
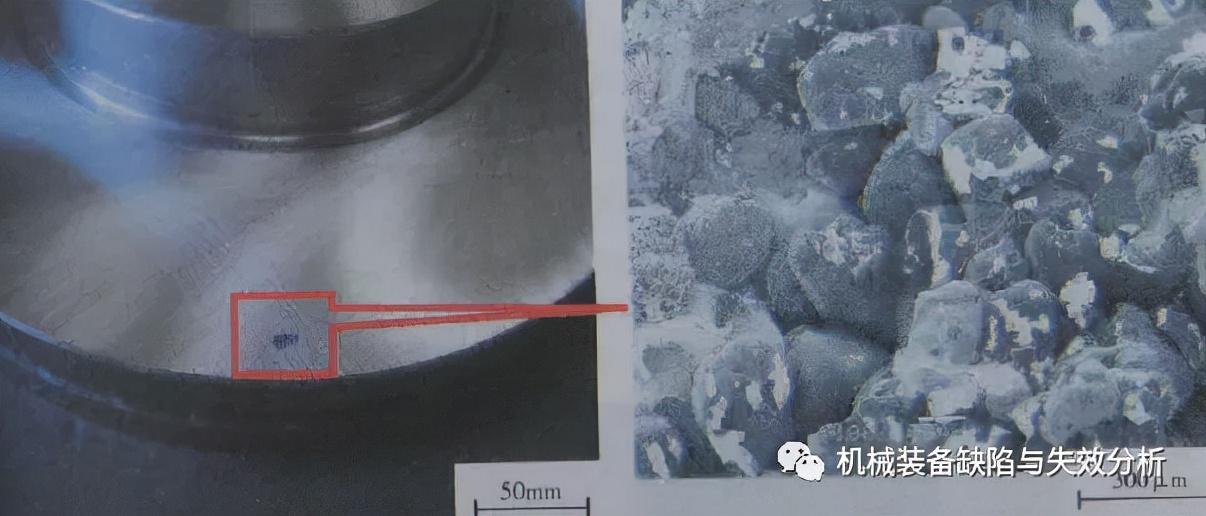
8.11 锡豆 锡青铜铸件的表面或内部孔洞中渗析出来的高锡低熔相豆粒状或汗珠状金属物。
8.12 硬点 在铸件的断面上出现分散的或比较大的硬质夹杂物,多在机械加工或表面处理时发现。
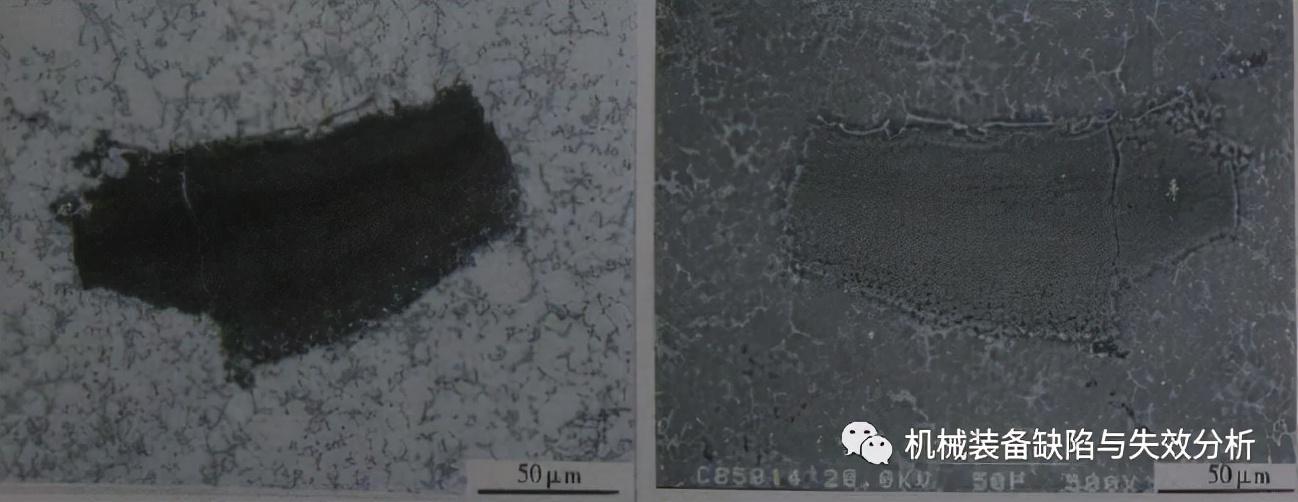
8.13 渣气孔 铸件浇注位置上表面的非金属夹杂物。
注:通常在加工后发现与气孔并存,孔径大小不一,成群集结。
九、成分、组织及性能不合格类缺陷
9.1 物理力学性能不合格 铸件的强度、硬度、伸长率,冲击韧度及耐热、耐蚀﹑耐磨等性能不符合技术条件的规定。
9.2 化学成分不合格 铸件的化学成分不符合技术条件的规定。
9.3 金相组织不合格 铸件的金相组织不符合技术条件的规定。
9.4 白边过厚 铁素体可锻铸铁件退火时因氧化严重在表层形成的过厚的无石墨脱碳层。
9.5 菜花头 由于溶解气体析出或形成密度比铸件小的新相,铸件最后凝固处或冒口表面鼓起,起泡或重皮的现象。
9.6 断晶 定向结晶叶片,由于横向温度场不均匀和叶片扭度较大等原因造成的柱状晶断续生长缺陷。
9.7 反白口 灰铸铁件断面的中心部位出现白口组织或麻口组织。
注:其外层是正常的灰口组织。
9.8 过烧 铸件在高温热处理过程中,由于加热温度过高或加热时间过久,使其表层严重氧化,晶界处和枝晶间的低熔点相熔化的现象。
注:过烧使铸件组织和性能显著恶化,无法挽救。
9.9 巨晶 由于浇注温度高﹑凝固慢,在钢锭或厚壁铸件内部形成的粗大的枝状晶缺陷。
注:高温轧制能破坏钢锭内的巨晶组织。扩散退火可以改善铸件内的巨晶组织。
9.10 亮皮 在铁素体可锻铸铁的断面上,存在的清晰发亮的边缘。缺陷层主要是由含有少量回火碳的珠光体组成。回火碳有时包有铁素体壳。
9.11 偏析 铸件或铸锭的各部分化学成分或金相组织不均匀的现象。
9.12 反偏析 与正偏析相反的偏析现象。
注:溶质分配系数K小于1且凝固区间宽的合金缓慢凝固时,因形成粗大枝品,富含溶质的剩余金属液在凝固收缩力和析出气体压力作用下沿枝晶间通道向先凝固区域流动,使溶质集中在铸锭或铸件的先凝固区域或表层,中心部分溶质较少。
9.13 正偏析 溶质分配系数K小于1的合金凝固时,凝固界面处一部分溶质被排出到液相中,随着温度的降低,液相中的溶质浓度逐渐增加,导致低熔点成分和易熔杂质从铸件外部到中心逐渐增多的区域偏析。
9.14 宏观偏析 铸件或铸锭中用肉眼或放大镜可以发现的化学成分不均匀性。
注:其分为正偏析,反偏析、V型偏析.带状偏析.重力偏析。宏观偏析只能在铸造过程中采取适当措施来减轻,无法用热处理和变形加工来消除。
9.15 微观偏析 铸件中用显微镜或其他仪器方能确定的显微尺度范围内的化学成分不均匀性。
注:其分为枝晶偏析(晶内偏析)和晶界偏析。晶粒细化和均匀化热处理可减轻这种偏析。9.9.16
9.16 重力偏析 在重力或离心力作用下,因密度差使金属液分离为互不溶合的金属液层﹐或在铸件内产生的成分和组织偏析。
注:减轻或防止重力偏析的方法有:浇注时充分搅拌,合金中加入阻碍初晶浮沉的元素,降低浇注温度加快凝固速度等。
9.17 晶间偏析(晶界偏析)晶粒本体或枝晶之间存在的化学成分不均匀性。
注:由合金在凝固过程中的溶质再分配导致某些溶质元素或低熔点物质富集晶界所造成。
9.18 晶内偏析(枝晶偏析) 固溶合金按树枝方式结晶时,由于先结晶的枝干与后结晶的枝干及枝干间的化学成分不同所引起的枝晶内和枝晶间化学成分差异。
注:枝晶偏析程度取决于合金凝固速度、偏析元素扩散能力和溶质的平衡分配系数。孕育处理和扩散退火可改善枝晶偏析。
9.19 球化不良 球墨铸铁件因原铁液含硫量高、采用球化剂不当,球化剂加入量不足或球化处理后停留时间过长而引起的石墨未球化或球化率过低的现象。
注:其特征是在铸件断面上,有块状黑斑或明显的小黑点,愈近中心愈密,金相组织中有较多的厚片状石墨或枝晶间石墨。
9.20 球化衰退 因铁液含硫量过高或球化处理后停留时间过长而引起的铸件球化不良缺陷。9.21 组织粗大 铸件内部晶粒粗大,加工后表面硬度偏低;渗漏试验时﹐会发生渗漏现象。
9.22 石墨粗大 铸铁件的基体组织上分布着粗大的片状石墨。机械加工后,可看到均匀分布的石墨孔洞。加工面呈灰黑色,断口晶粒粗大。
注:有这种缺陷的铸件,硬度和强度低于相应牌号铸铁的规定值。气密性试验时会发生渗漏现象
9.23 石墨集结 在加工大断面铸铁件时表面上充满石墨粉且边缘粗糙的部位。注:石墨集结处硬度低,且渗漏。
9.24 铸态麻口 可锻铸铁件的一种金相组织缺陷。其断口退火前白中带灰,退火后有片状石墨,降低铸件的力学性能。
9.25石墨漂浮 在球墨铸铁件纵断面的上部存在的一层密集的石墨黑斑。
注:和正常的银白色断面组织相比,有清晰可见的分界线。金相组织特征为石墨球破裂,同时缺陷区富有含氧化合物和硫化镁。
9.26 表面脱碳 铸钢件或铸铁件因充型金属液与铸型中的氧化性物质发生反应,使铸件表层含碳量低于规定值。
- 本文分类:常识
- 本文标签:无
- 浏览次数:100 次浏览
- 发布日期:2024-09-29 08:39:20
- 本文链接:https://m.ghbk.net/changshi/Md8JvAZq6x.html